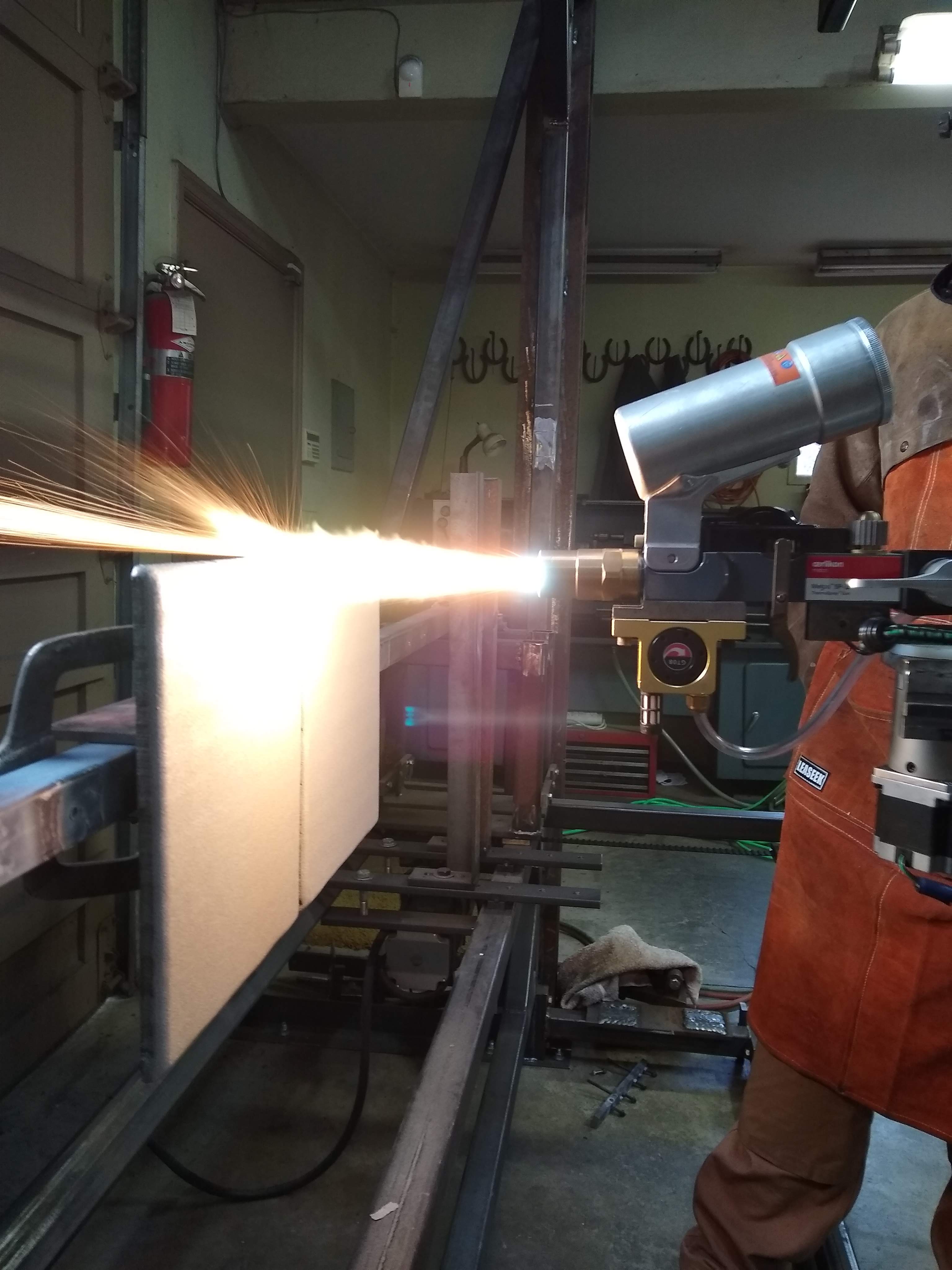
Hardfacing
Thermal Spray and Weld Overlay
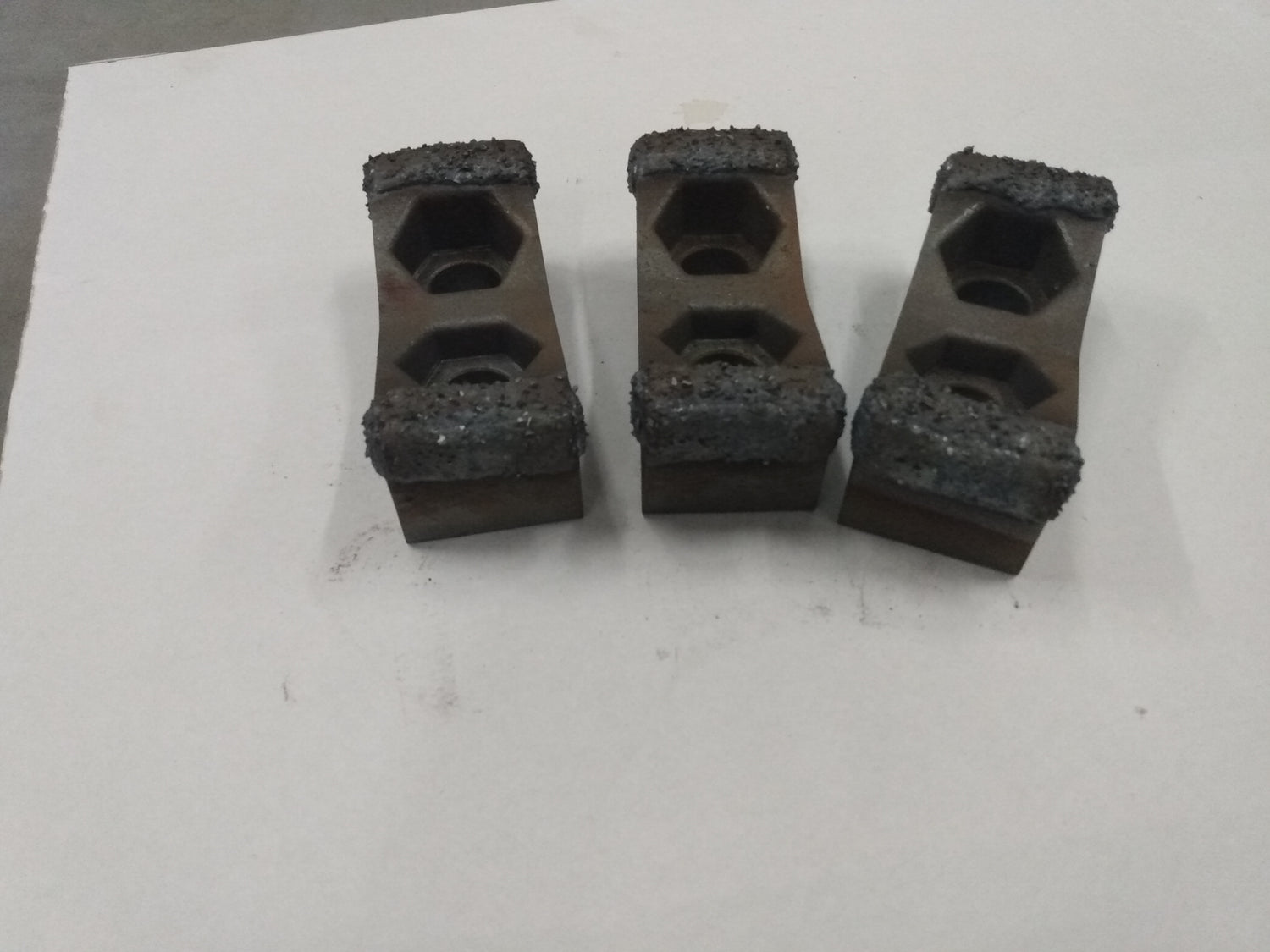
Why not just have your local welder hardface for you?
Would you trust a general practitioner with brain surgery?
While many welders can perform basic hardfacing, achieving optimal results requires specialized expertise and equipment. Hardfacing isn't just welding. It's a science and an art that demands a deep understanding of materials, wear patterns, and industry-specific challenges. Pi Fabricators has honed this expertise over years of dedicated hardfacing work. When you choose us, you're not just getting a quick fix; you're investing in a solution designed for maximum performance and longevity.
Are you losing customers because the competition offers longer lasting wear parts?
You should not lose your consumables business because your parts wear out too fast.
End user of hardfaced parts? No problem. We serve you too!
The right hardface helps grow your business in 3 ways
-
1. Your customer's parts last longer.
-
2. Your customer is happy.
-
3. Your customers come back to you and your business grows.
Don't just take our word for it. Here's what one of our customers has to say
"We were struggling with the short lifespan of wear cups in our high-temperature (1200°F) environment. Pi Fabricators wear cups consistently last over 4 months, a massive leap compared to the 1 month we got from OEM parts. This has not only saved us money but also improved our overall efficiency."
Nick Avenetti, President, Supreme Perlite, Portland OR
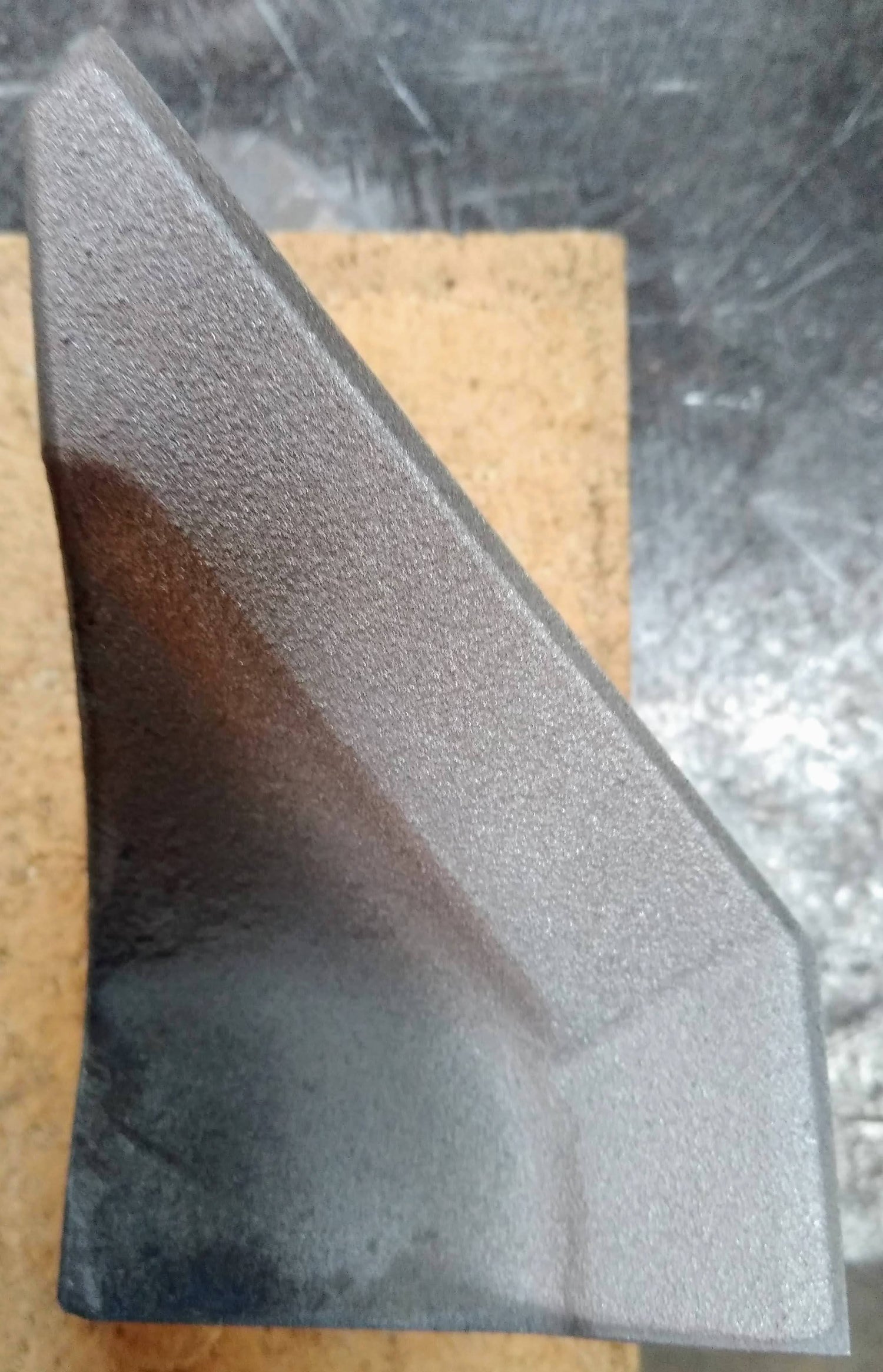
Thermal Spray
Pi Fabricators offers CNC machine applied and manually applied spray and fuse thermal sprayed coatings.
These coatings are smooth as applied and are metallurgically bonded so that delamination is not a concern.
Options include corrosion resistant nickel based superalloys as well as iron based coatings.
Most parts are thermally sprayed on our CNC thermal spray machine and fused in a controlled atmosphere furnace. But some parts may need to have thermal spray hand applied.
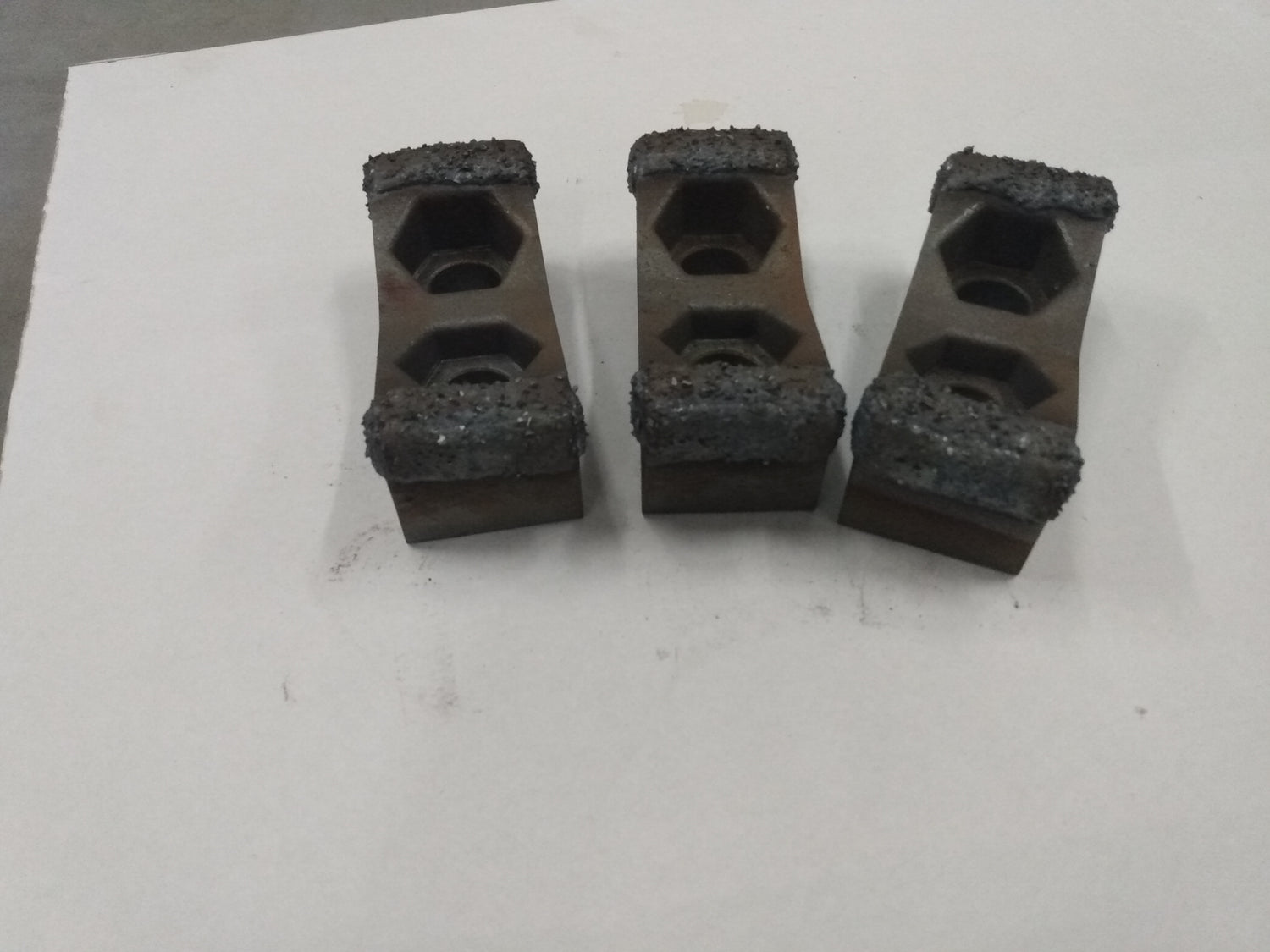
Weld Overlay
Weld overlay is an excellent and cost effective option for applications where a completely smooth hardface is not required.
We offer MIG tungsten carbide embedding (Also known as drop carbide and embedded carbide) hardface as well as chrome carbide and other hardfacing technology depending on your application requirements.
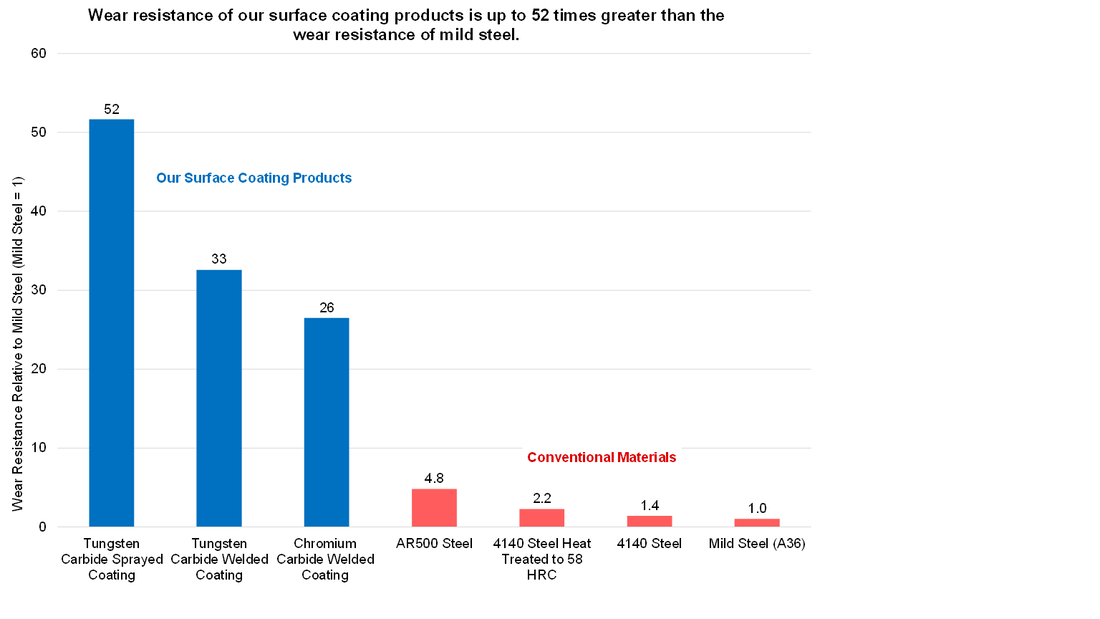
Our Hardface lasts a lot longer than conventional materials.
Up to 52x greater wear resistance than mild steel under ASTM G65 (abrasive sand wheel test) wear conditions.
Get the right hardface on your parts today
-
1. Click "Contact Us"
-
2. Email us your drawings, order qt and application or give us a call.
-
3. We will make a hardface recommendation and give you a quote.
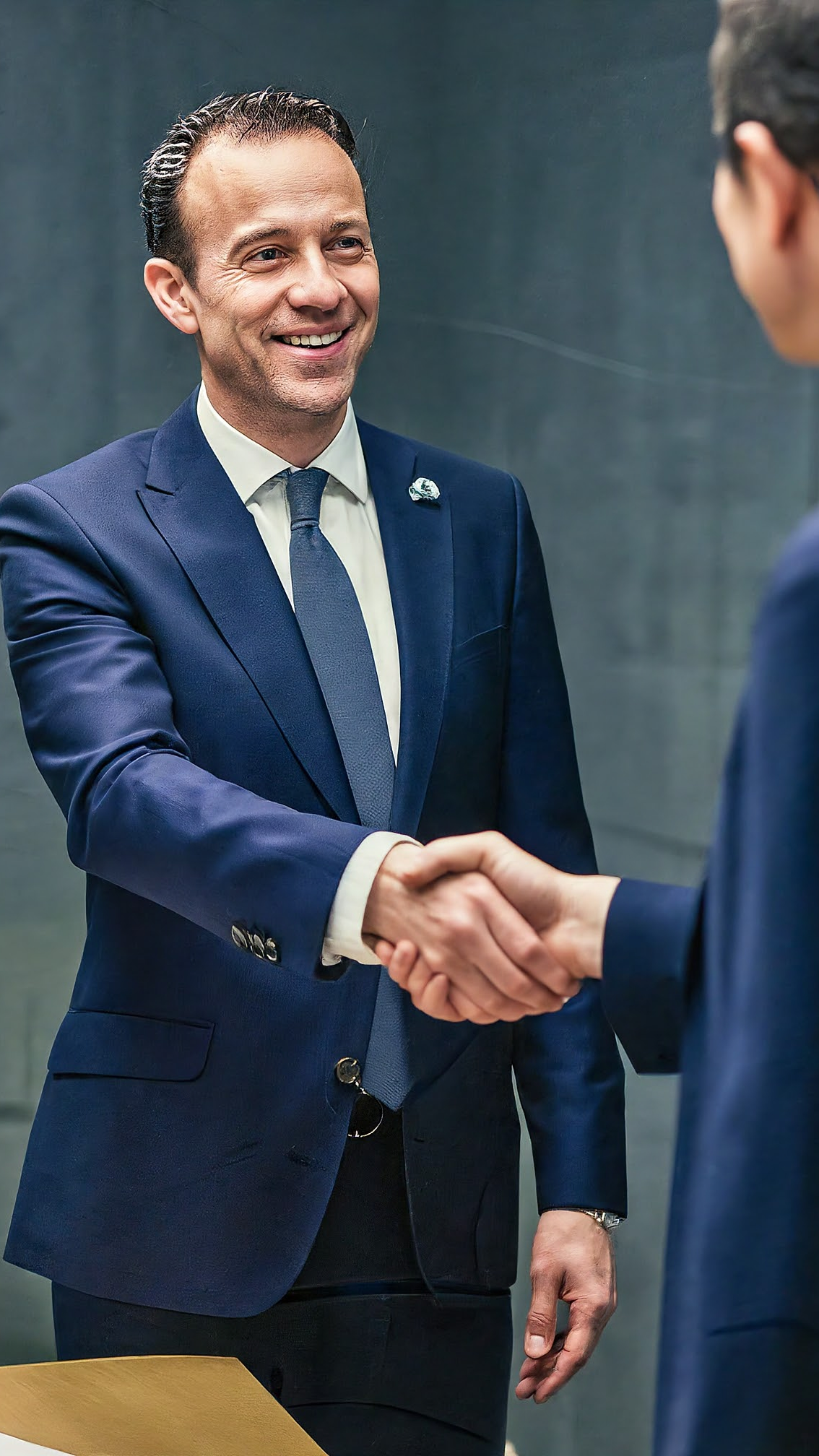
Keep your customers coming back
At Pi Fabricators we know that you want to have hardface applied to your wear parts that meet your customer needs. In order to do that, you need the right custom hardfacing at the right price. The problem is it is hard to know which hardface solution to choose which leads to parts that don't meet your customer needs and lost business. We believe you should not lose business because your consumable don't have the right hardface. We understand the importance of using the right hardface for your application which is why we offer multiple hardface technologies.
Here's how you can get the right hardface solutions for your parts:
1) Click "Contact Us".
2) Email us your drawings, order qt and application or give us a call.
3) We will make a hardface recommendation and give you a quote.
Here are some examples of hardfaced parts we make for our customers.
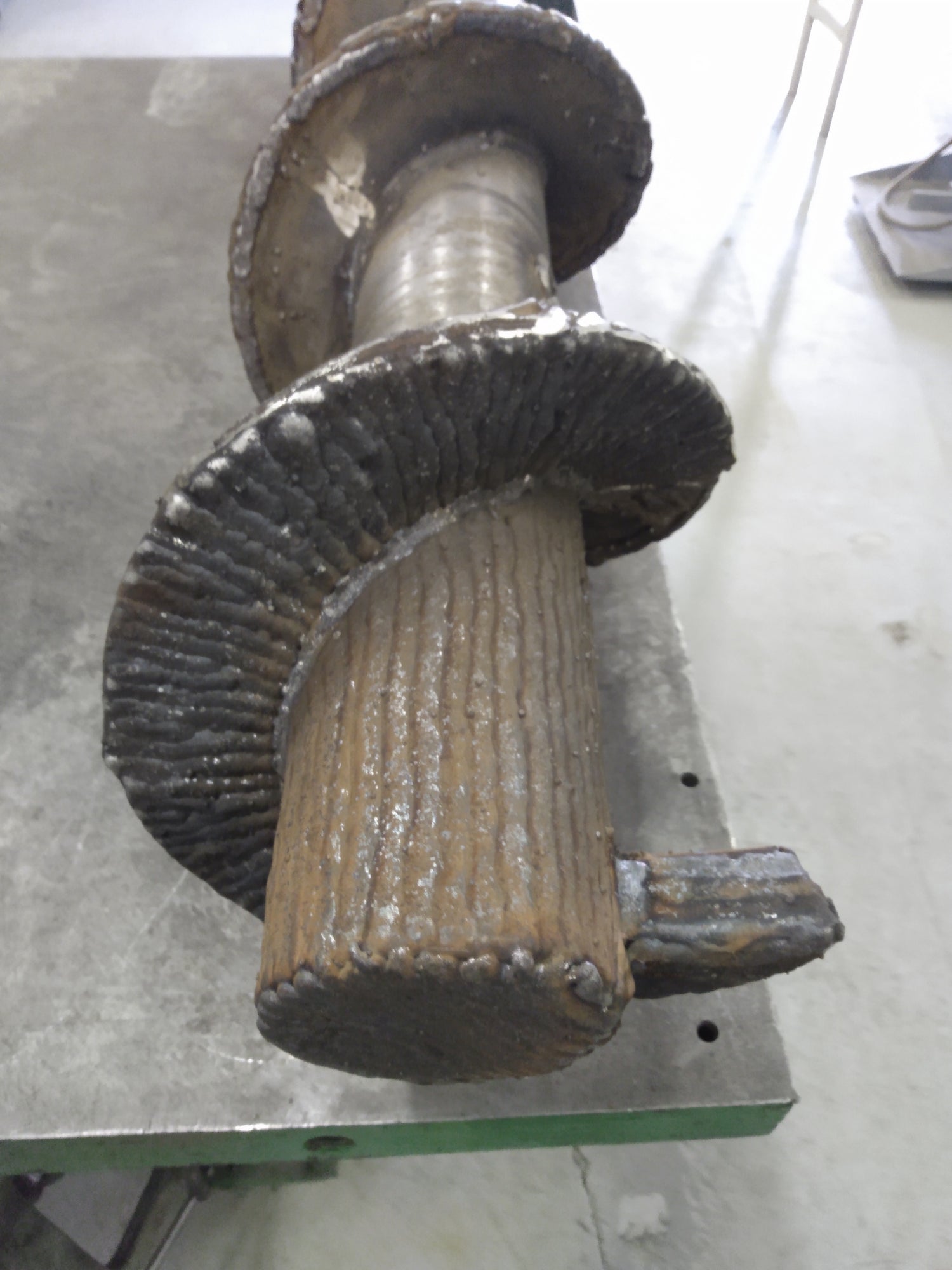
Hardfaced auger for bottle recycling
Recycling is a tough job that wears augers out fast.
We offer hardfacing options that have proven themselves in the field.
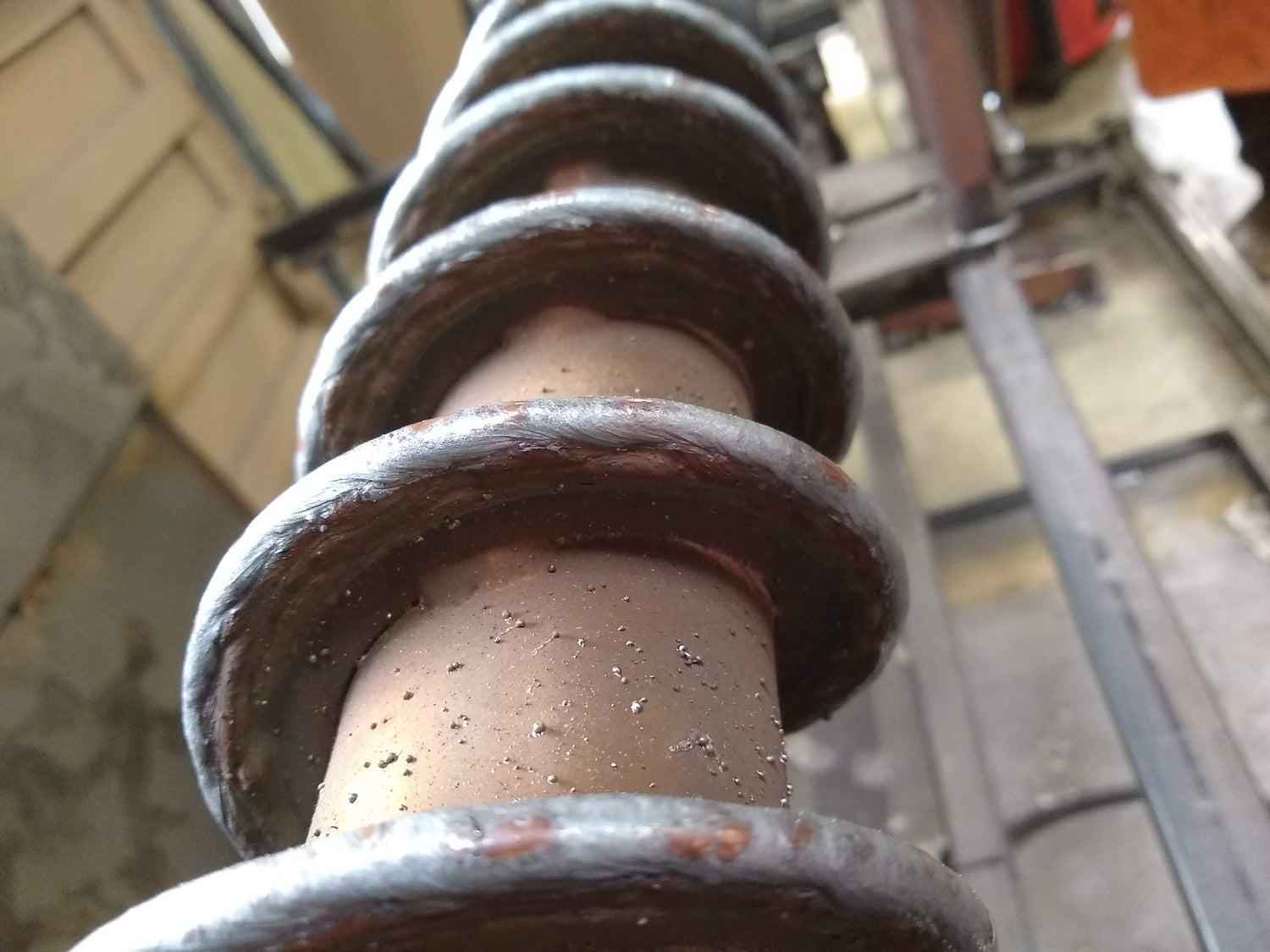
Auger Rebuilt for Perlite processing plant
Perlite (the little white rocks in potting soil) is an abrasive media. To make wear even greater perlite is processed at high temperatures. This requires hardface that can take the heat. We have the knowledge to select the right alloy for your high temperature wear applications.
We have applied hardface alloys rated to resist wear up to 1400F (760C).
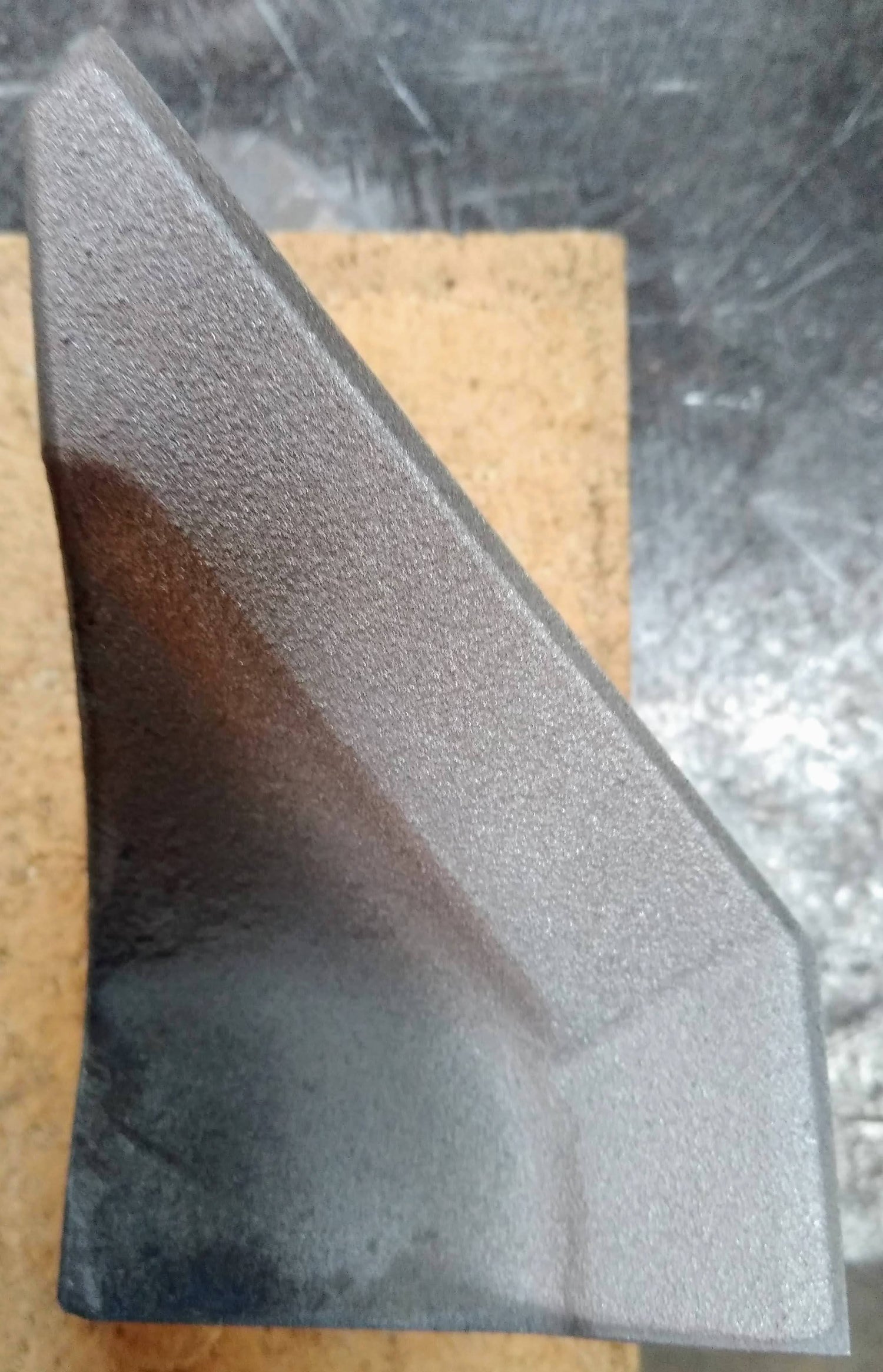
Thermal spray and fuse
Our customer needed a smooth long wear life hardface for a chipper knife holder in the wood products industry. We were able to offer a thermal sprayed nickel superalloy with tungsten carbide reinforcement. Not only that, at the customers request, we were able to apply variable CNC controlled thickness to the coating so the coating was thicker at the point of maximum wear.
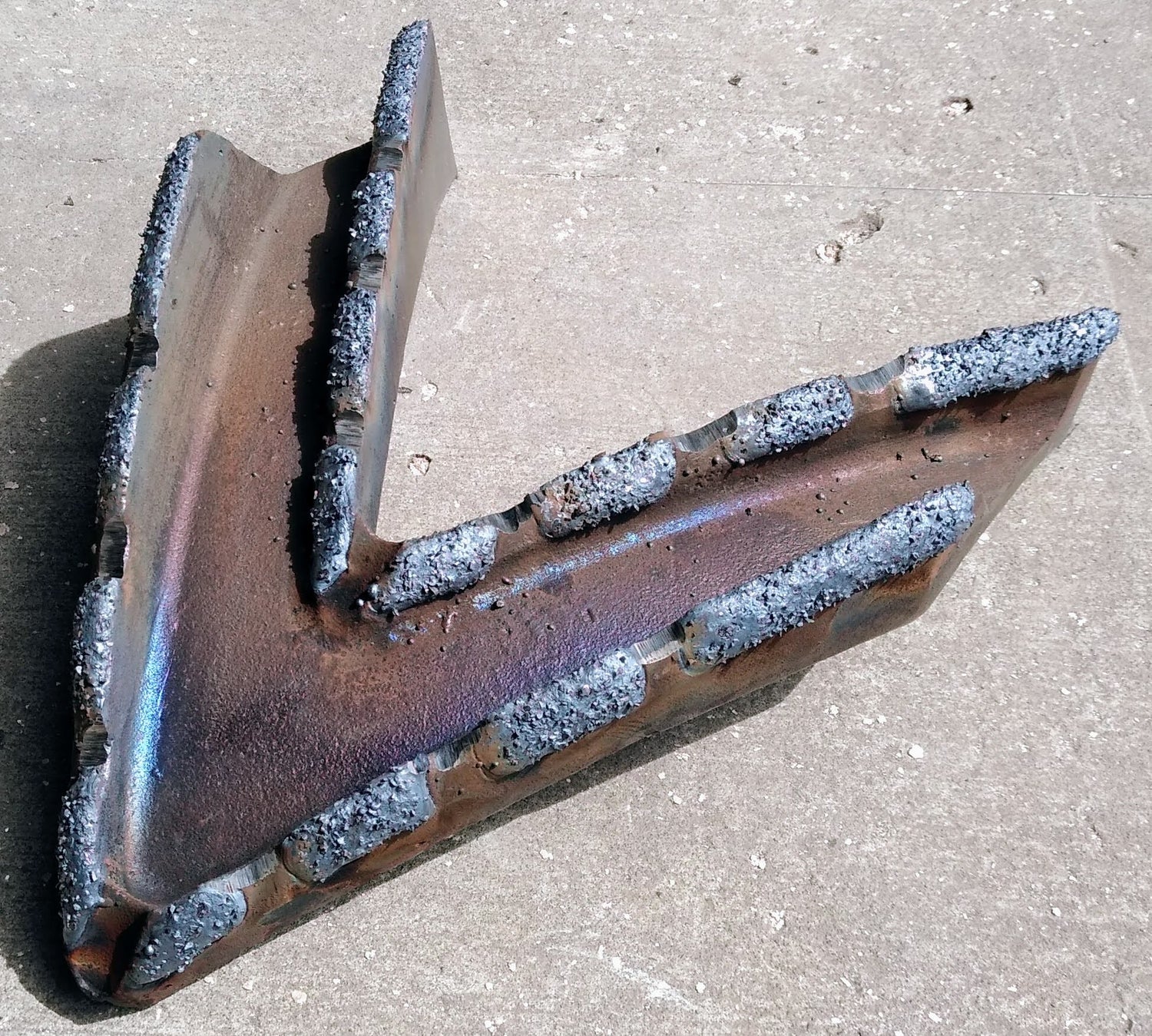
Embedded carbide
Handling logs is a tough business. We were able to offer our customer an embedded carbide (drop carbide) hardface that dramatically increased the wear life of their debarker flights.
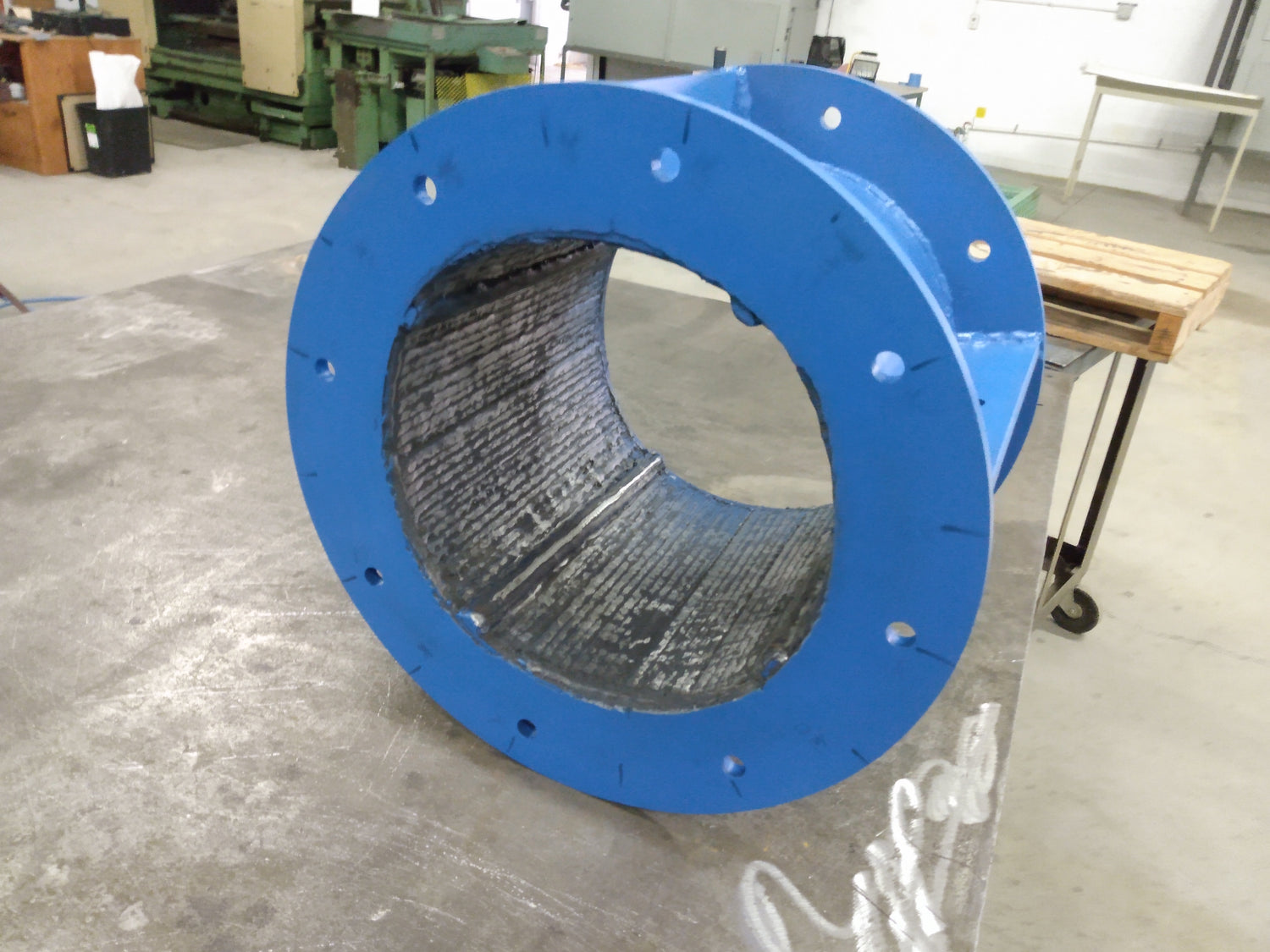
Hardfaced Compaction Tube
Hardfaced Compaction tube for the recycling industry.