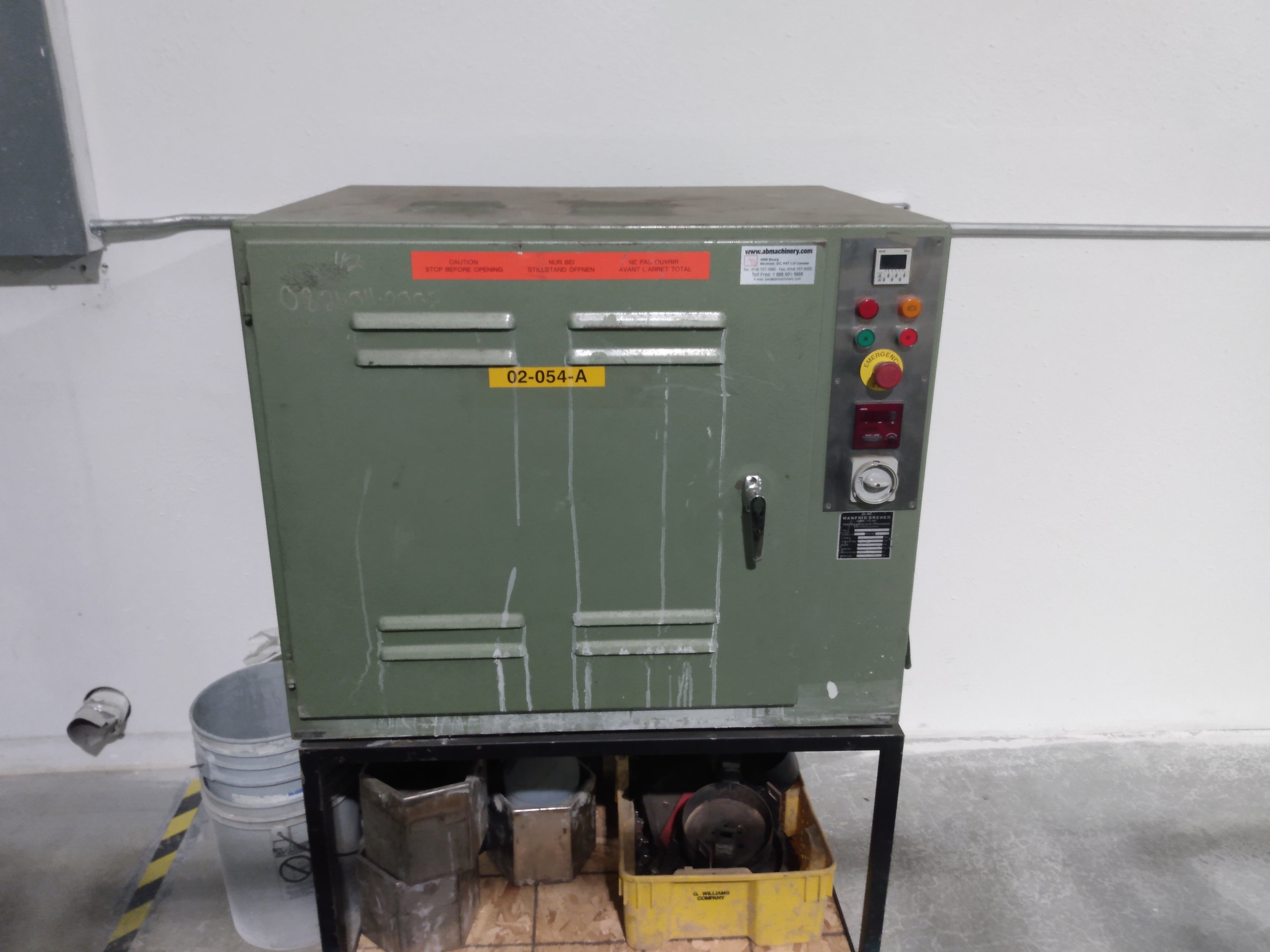
Mass Finishing
Tumble Blasting, Centrifugal Barrel Tumbling
Are you tired of:
Spending too much labor finishing your parts?
You should not be forced to manually finish parts when there are cost effective mass finishing options.
Lower your costs
-
Lower Labor Costs
Parts finished for you at a fraction the cost of the labor to finish them in house.
-
Low Minimums
With order minimums as low as $50 for mass finishing you can get your parts finished cost effectively even at low volume.
-
Convenient location
Conveniently located 3 miles from I-5 in Salem Oregon
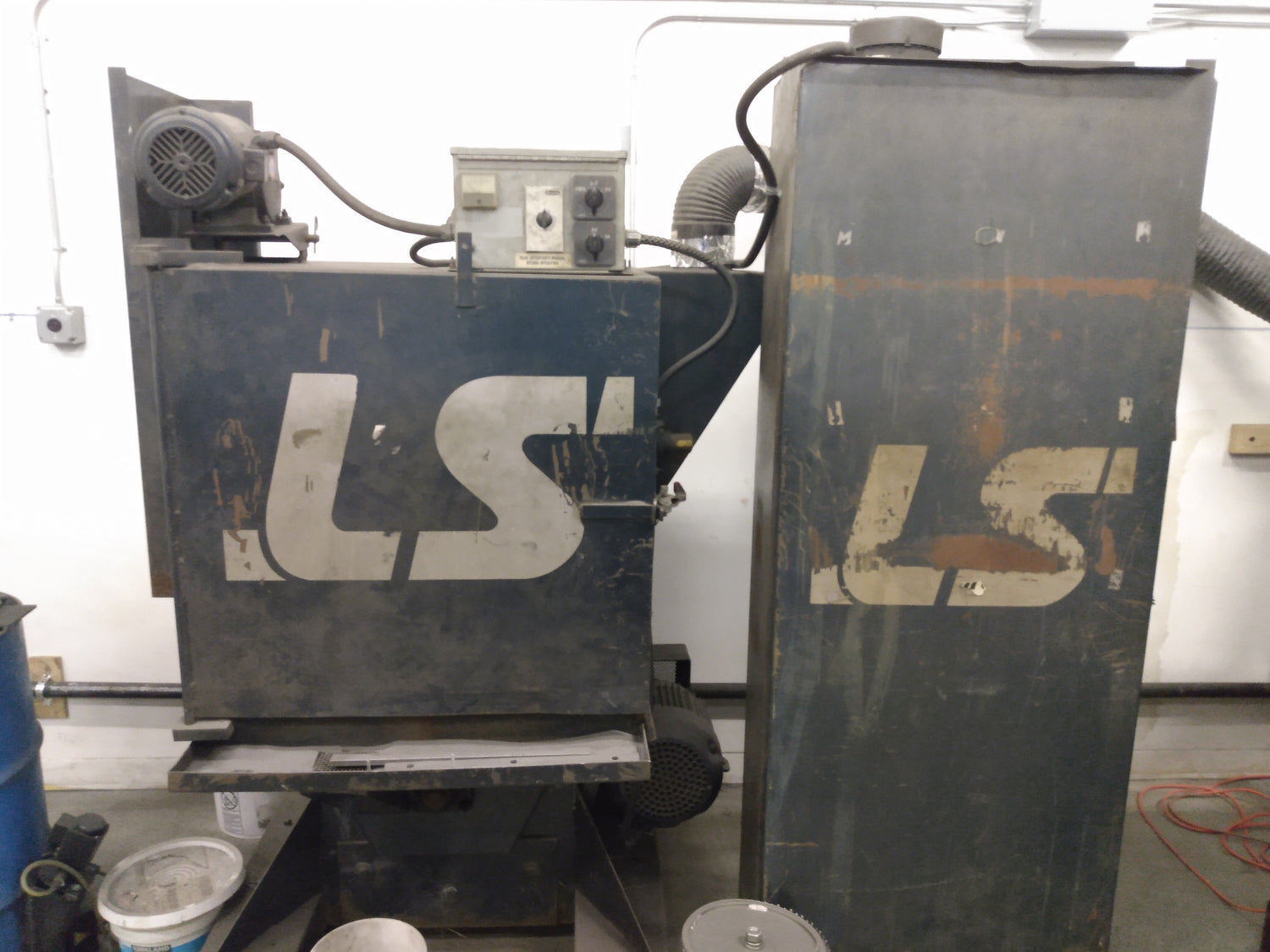
Mass finishing is consistent
- Controlled Process Parameters: Mass finishing machines operate with precise control over speed, media type and size, compound selection, and cycle times. This ensures each batch receives identical treatment.
- Uniformity Across All Parts: The tumbling or tumble blasting action in mass finishing means every surface of every part gets equal exposure to the finishing media, guaranteeing a consistent result throughout the batch.
- Elimination of Human Error: Manual finishing is subject to inconsistencies based on operator skill, fatigue, and individual technique. Automated mass finishing removes these variables.
- Repeatability: Mass finishing recipes can be saved and replicated exactly. If you need the same finish a month from now, it's easily achieved. Manual finishing is far harder to perfectly duplicate.
We used to spend a lot of labor finishing parts too. So we understand you.
We used to hand blast and deburr small parts.
With our small part count and labor costs rising we invested in mass finishing technology to slash our labor inputs.
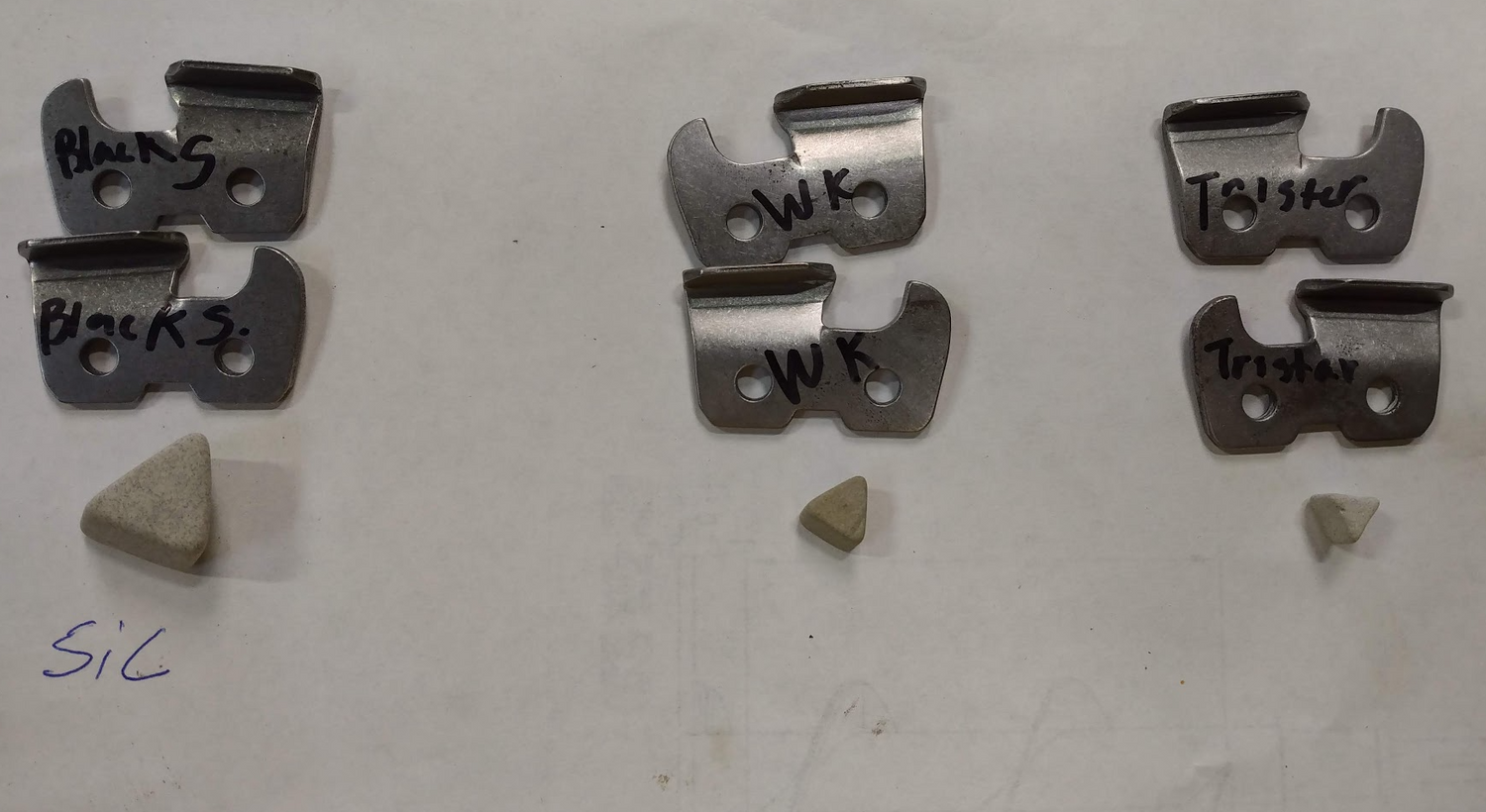
Quality that scales
- Reduced Inspection Time: The predictable results of mass finishing reduce the need for extensive part-by-part inspection, saving time and resources.
- Scalability: Mass finishing can easily be scaled up to handle larger volumes, maintaining consistency even as production increases.
- Better Surface Quality Control: Mass finishing offers fine-grained control over surface finishes, from rough deburring to very smooth, polished results. This control is harder to achieve with manual methods.
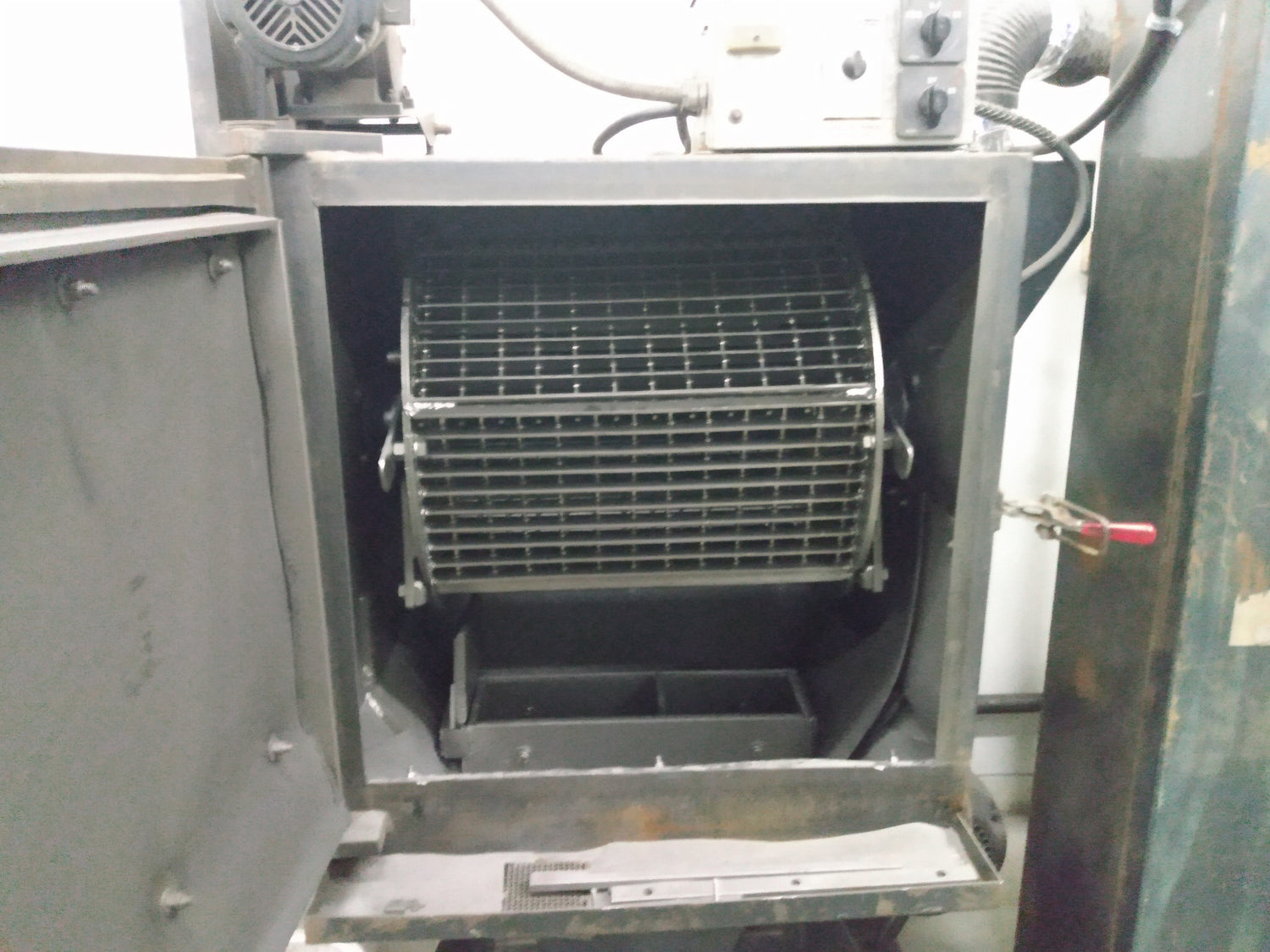
Lower your finishing costs
At Pi Fabricators we know that you need your small parts deburred and finished at an affordable rate. In order to do that, you need a supplier with mass finishing equipment. The problem is not many shops have mass finishing equipment and those that do often have high minimums which leads to you spending valuable labor hours hand finishing small parts. We believe you should be able to have your parts cost effectively mass finished. We understand the importance of using your labor efficiently which is why we offer mass finishing with low order minimums.
Here's how you can get your parts mass finished:
1. Click "Contact Us".
2. Email us or give us a call to describe the part you need finished.
3. We will quote the job.
You can select from a multitude of surface finishes
Polished
Aggressively deburred with rounded edges
Peened surface
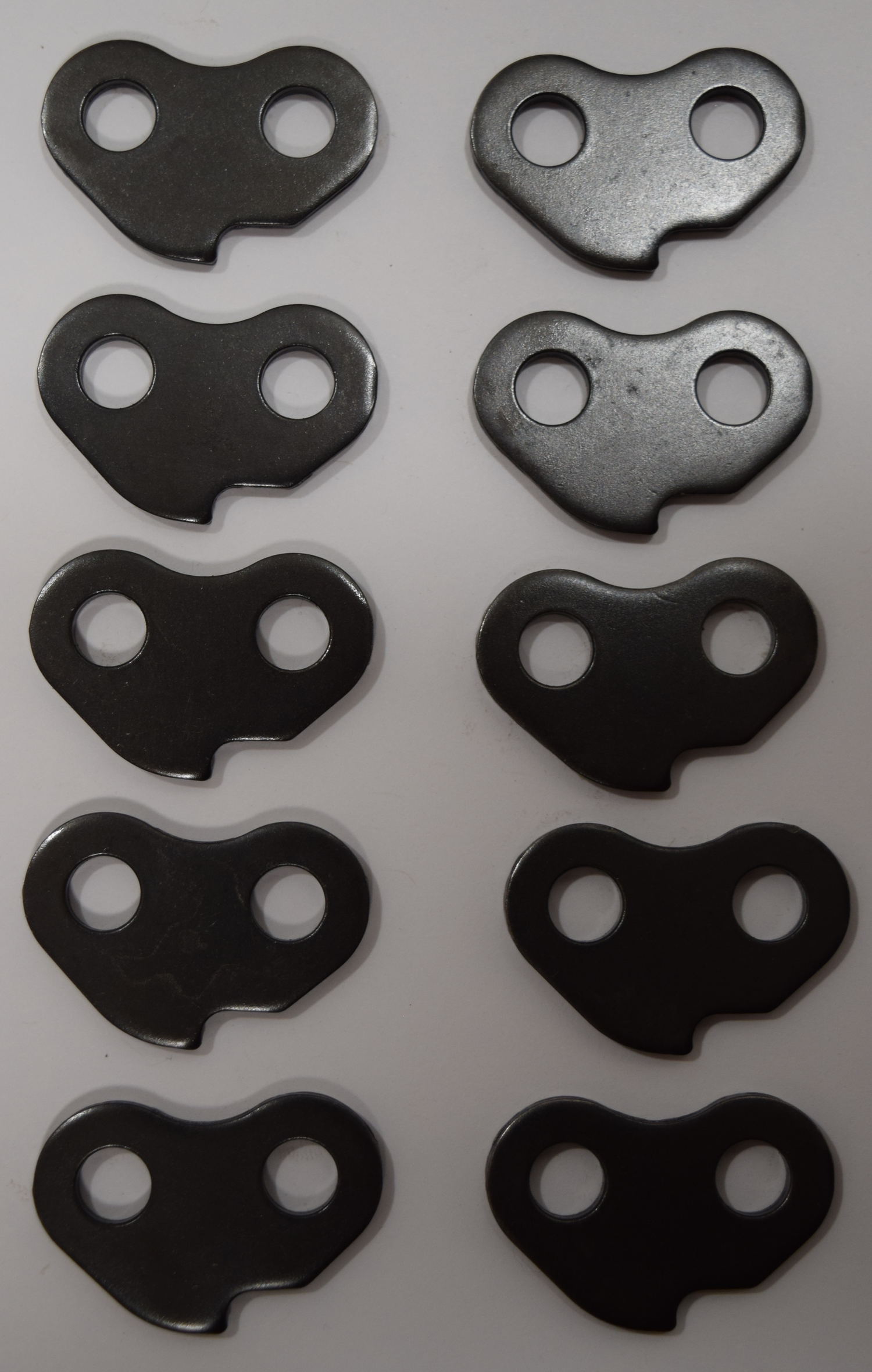
Shot Peening Small Parts with Tumble blasting
Tumble blasting can be used to shot peen your small parts. This can significantly improve the fatigue life of your steel parts by introducing compressive residual stress into the surface layer. Here's how it works:
- Surface Bombardment: Shot peening bombards the steel surface with small spherical metallic, ceramic, or glass beads. The force of the impact creates tiny indentations on the surface.
- Compressive Stress Generation: These indentations don't just leave marks, they force the metal to compress beneath the impact zone. This creates a layer of compressive residual stress below the surface.
- Resistance to Crack Initiation: During regular operation, steel parts experience cyclic loading, which can cause microscopic cracks to initiate at the surface. The compressive stress layer in shot peening acts like a shield, counteracting the pulling forces (tensile stress) that tend to open these cracks.
- Slower Crack Growth (if present): Even if a small crack manages to form, the compressive stress field can slow its growth. This gives the material more time to resist failure and allows for earlier detection during inspections.
Cost-Effective Pre-Weld Prep
Tumble blasting offers a cost-effective solution for pre-weld preparation for small parts such as gussets. By automating the removal of contaminants, rust, and mill scale, tumble blasting significantly reduces the manual labor typically required for these tasks. This automation leads to faster turnaround times and lower labor expenses, making it a budget-friendly choice for achieving clean and weld-ready surfaces.