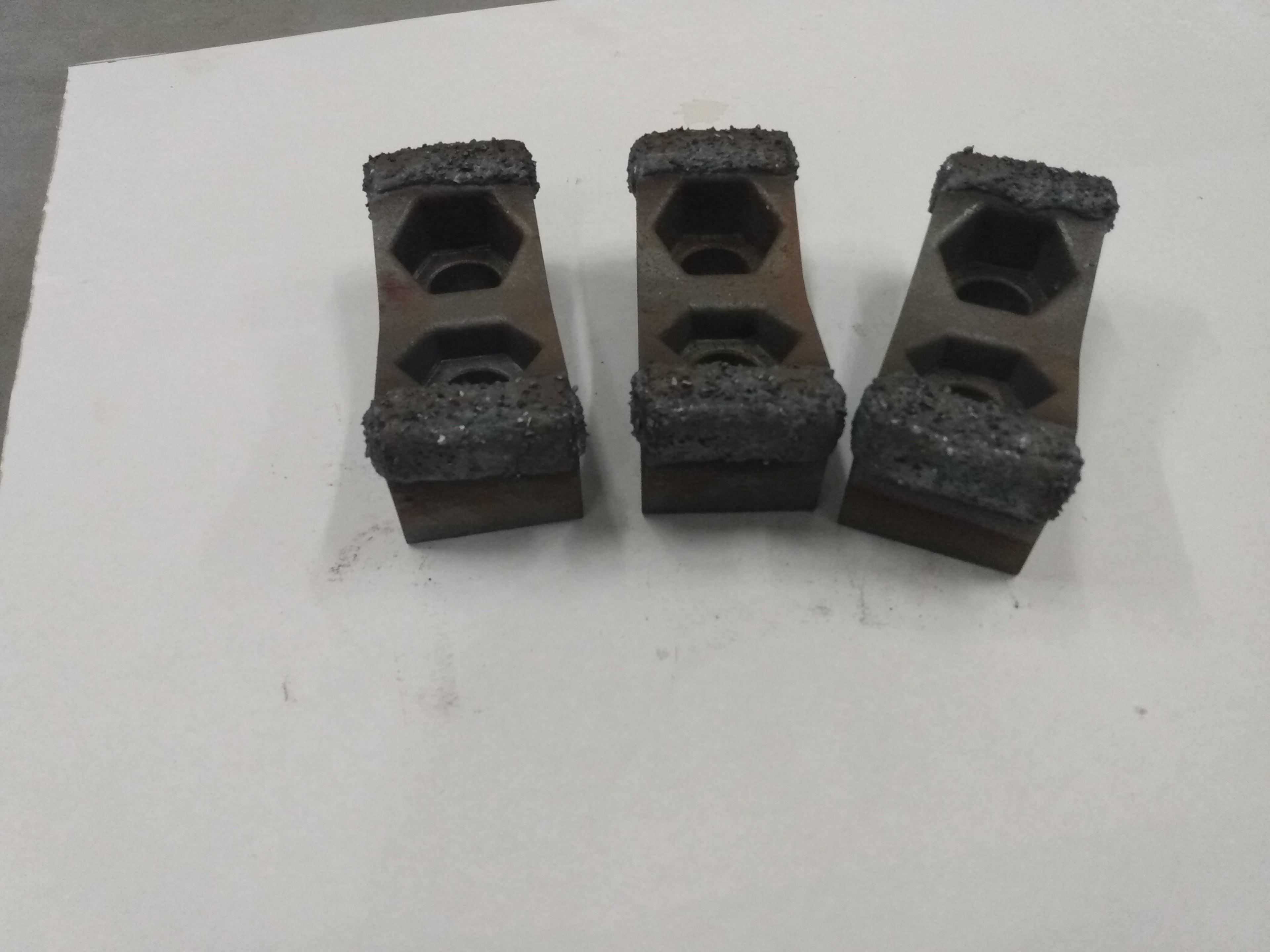
MIG Tungsten Carbide Embedding
Unmatched Wear Resistance at a Competitive Price
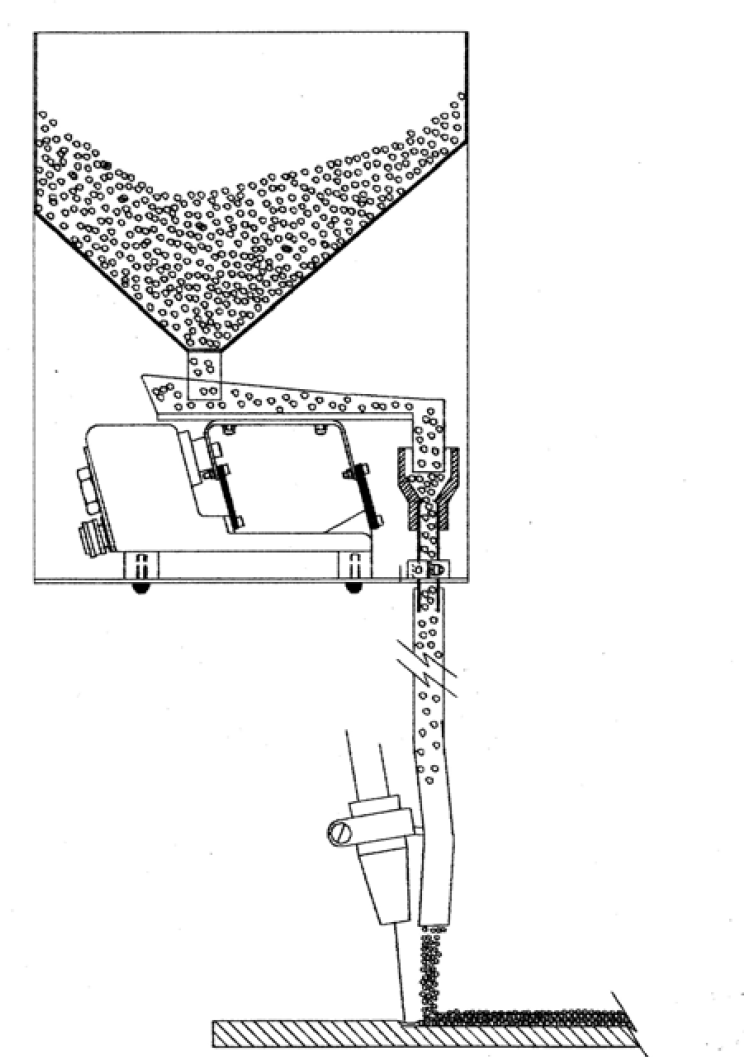
What is MIG tungsten carbide embedding?
MIG tungsten carbide embedding, also known as embedded carbide and drop carbide, is a specialized welding technique used to enhance wear resistance of parts. The process involves dropping carbide grit into the molten weld pool during welding. These carbide particles become embedded in the weld metal as it solidifies, creating a composite material that is tough and wear resistant.
MIG tungsten carbide embedding often offers the highest value relative to its wear resistance for applications requiring low dimensional tolerance.
MIG Tungsten Carbide Embedding - Cost Calculator
Estimate the cost to have your parts hardfaced with drop carbide.
Assumptions about calculated price:
- MIG tungsten carbide embedding hardface provided by Pi Fabricators costs between $1.72 per square inch up to $2.97 per square inch (subject to a $50 minimum order quantity). Larger surface areas per part and larger total surface area for an order lead to lower per square inch cost.
- Price is calculated assuming use of a tool steel matrix with 10-30 mesh (0.0232 inches to 0.0787 inches in diameter) crushed tungsten carbide. Other matrix metals and mesh sizes are available upon request.
- The Calculated price assumes parts are clean and do not require prep such as, for example, mill scale removal. Pi Fabricators offers in house mass finishing and abrasive blasting to cost effectively prep parts if required.
- Heavy parts with a small surface area to be coated will cost more than shown in this cost calculator for a given surface area due to extra handling costs as well as increased preheating time.
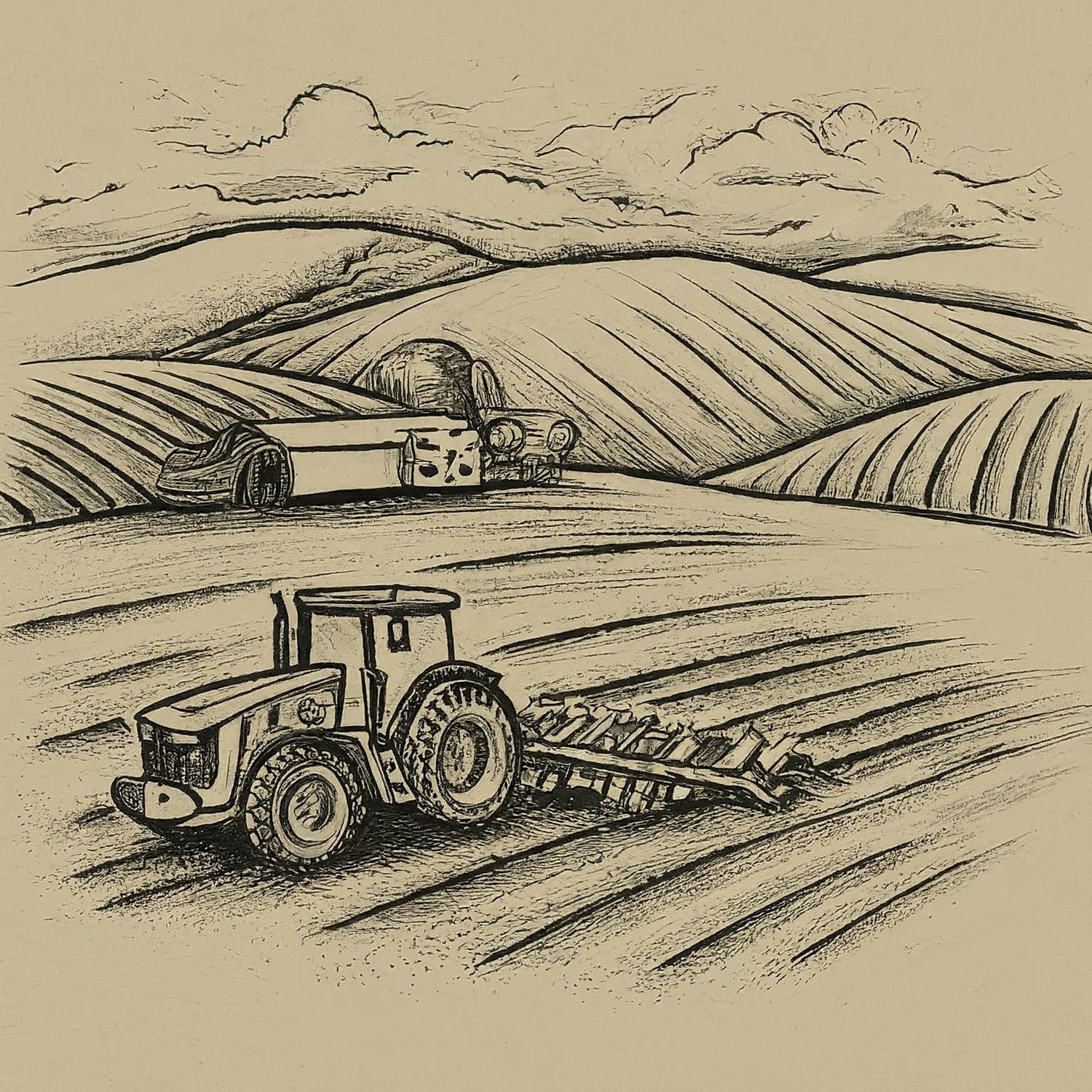
What industries use MIG tungsten carbide embedding hardface?
The reality is MIG tungsten carbide embedding is useful and often the highest value option in any low tolerance high wear application. But here are a few examples of industries that benefit from MIG tungsten carbide embedding hardface:
- Agriculture
- Logging / Wood Products
- Recycling
- Mining
- Oil & Gas
- Construction
- Manufacturing
The advantages of a tool steel matrix
We have chosen to make our standard offering of MIG tungsten carbide embedding hardface with a tool steel matrix. A tool steel matrix helps MIG tungsten carbide embedding overlay outlast MIG tungsten carbide embedding with just a carbon steel matrix by a factor of 2 to 8 depending on the application.
The primary wear mechanism for MIG tungsten carbide embedding hardface is through the matrix wearing out around the carbide particles and the carbide particles eventually falling out once there is no more metal to hold them in place. By using a tool steel matrix on your parts the tool steel is much more wear resistant relative to carbon steel so this slows down the process of the matrix wearing out around the carbide particles and dramatically increases the wear life of the hardface.

Why does MIG Tungsten Carbide Embedding offer such a high return on investment?
By using recycled tungsten carbide and relatively cost effective tool steel welding wire (as compared to more exotic hardfacing metals) MIG tungsten carbide embedding hardface delivers extreme wear resistance at a competitive price.
Three advantages of Pi Fabricators' MIG Tungsten Carbide Embedding process vs conventional:
-
Extreme Abrasion Resistance:
Experience the pinnacle of abrasion protection. Our process embeds tungsten carbide particles, with a hardness of 70 HRC, within a robust tool steel matrix, with a hardness range of 55-60 HRC, delivering exceptional wear resistance that outperforms conventional MIG Tungsten Carbide Embedding by more than 2 times. This translates to significantly extended equipment life and reduced maintenance costs.
-
Cost-Effective Solution:
Achieve superior wear protection without breaking the bank. Pi Fabricators MIG Carbide Embedding process is not only more durable but also is offered at a more competitive cost than most other shops, even when compared to shops offering conventional mild steel MIG tungsten carbide embedding. At Pi Fabricators You get the best of both worlds – top-tier performance and cost savings.
-
Evenly Dispersed Tungsten Carbide:
By using specialty tool steel welding wire Pi Fabricators achieves a fluid and clean weld puddle during the welding process. This fluid and clean weld puddle helps the tungsten carbide grit to more evenly disperse throughout the weld puddle while the tool steel is still a liquid maximizing the effectiveness and wear life of the hardface produced by the embedding process.
Application Examples
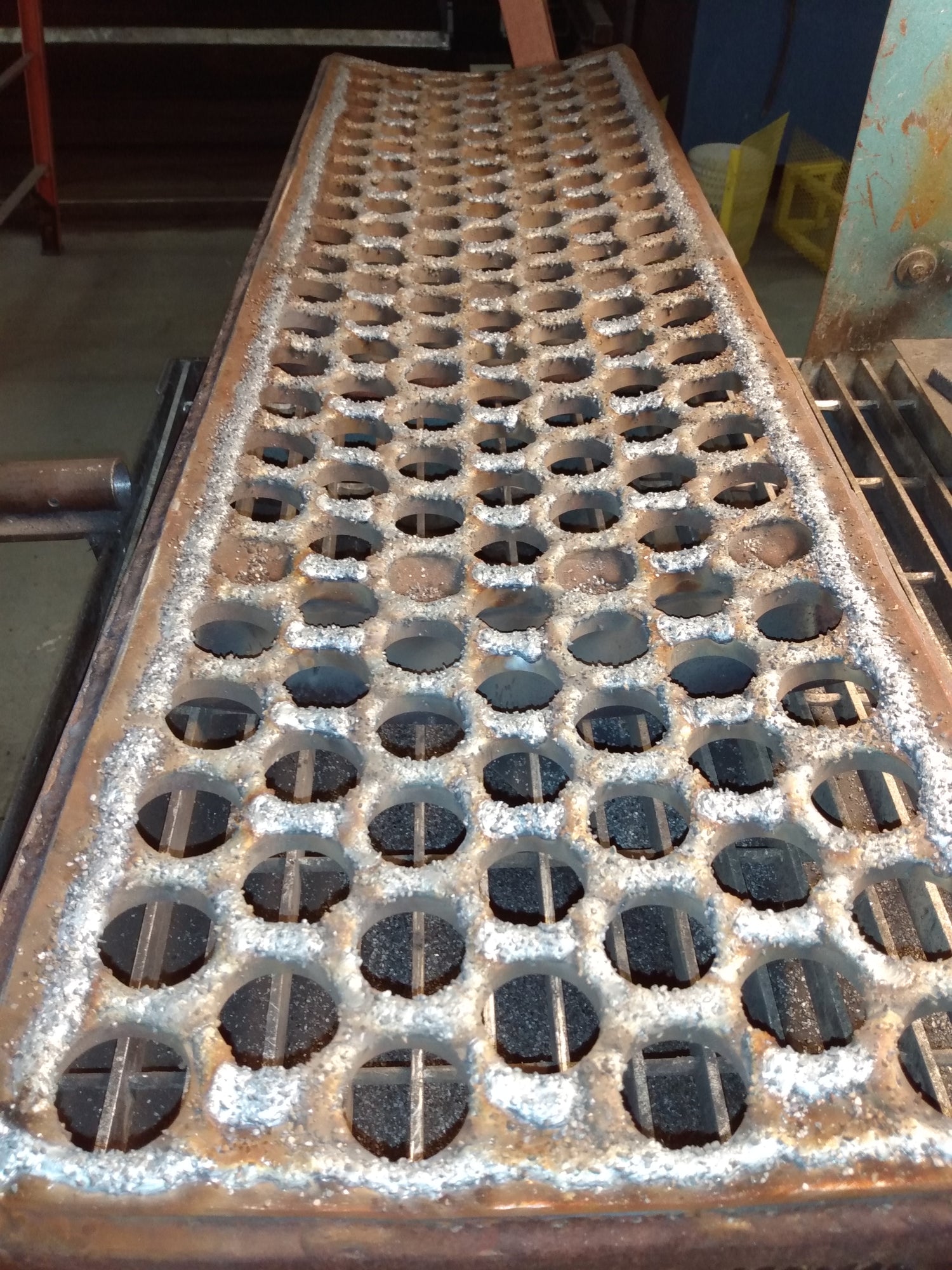
Wood Hog Grate
Pi Fabricators applied embedded carbide to this hog grate for our customer. This is an example of an application where long wear life is required but fine tolerances or finish grinding/machining is not required.
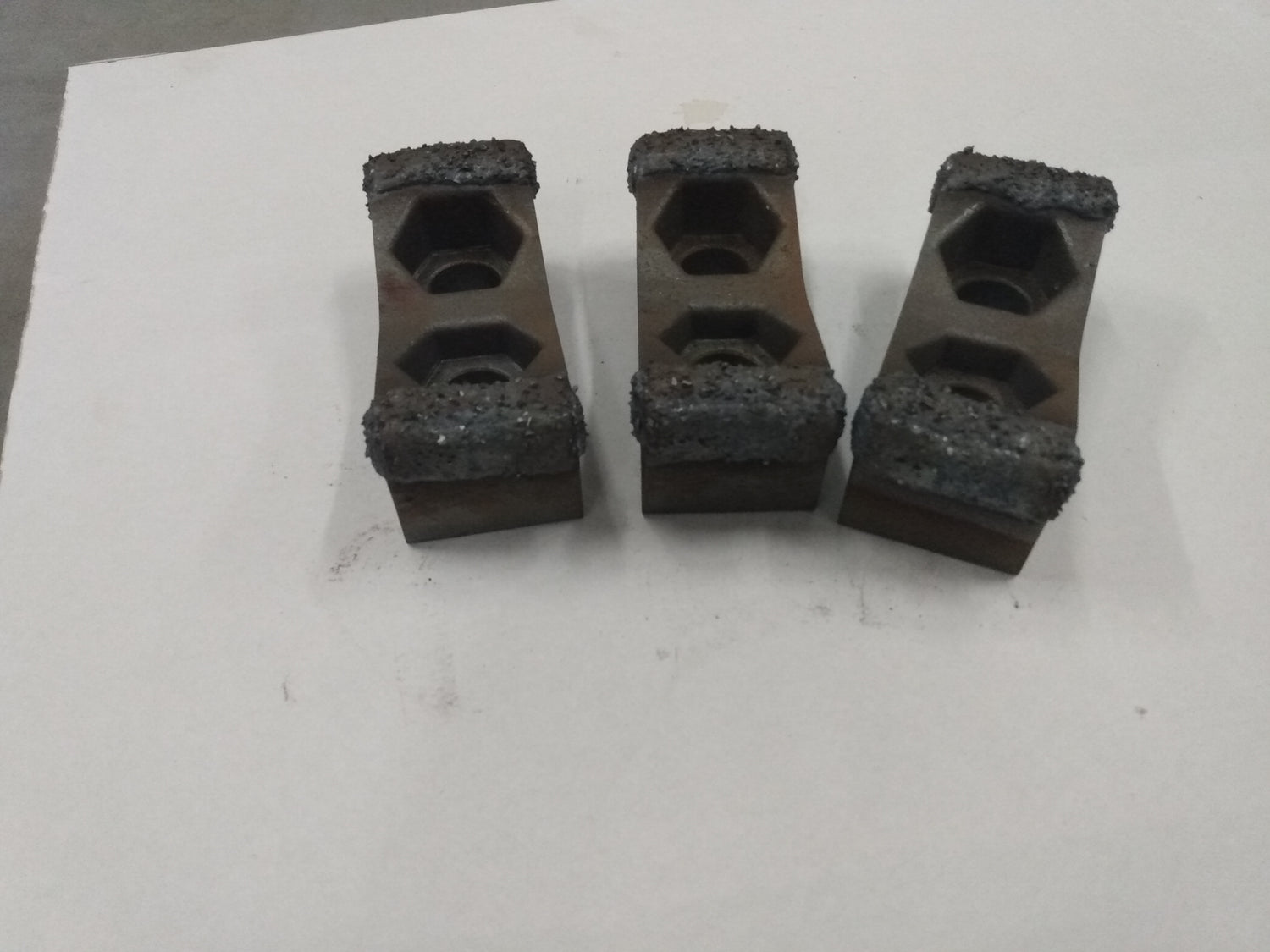
Hammer Mill Hammers
Pi Fabricators applies embedded carbide to hammers for hammer mill hammers. While many orders are for more than 1000 hammers at a time we can also process small orders including for end users.
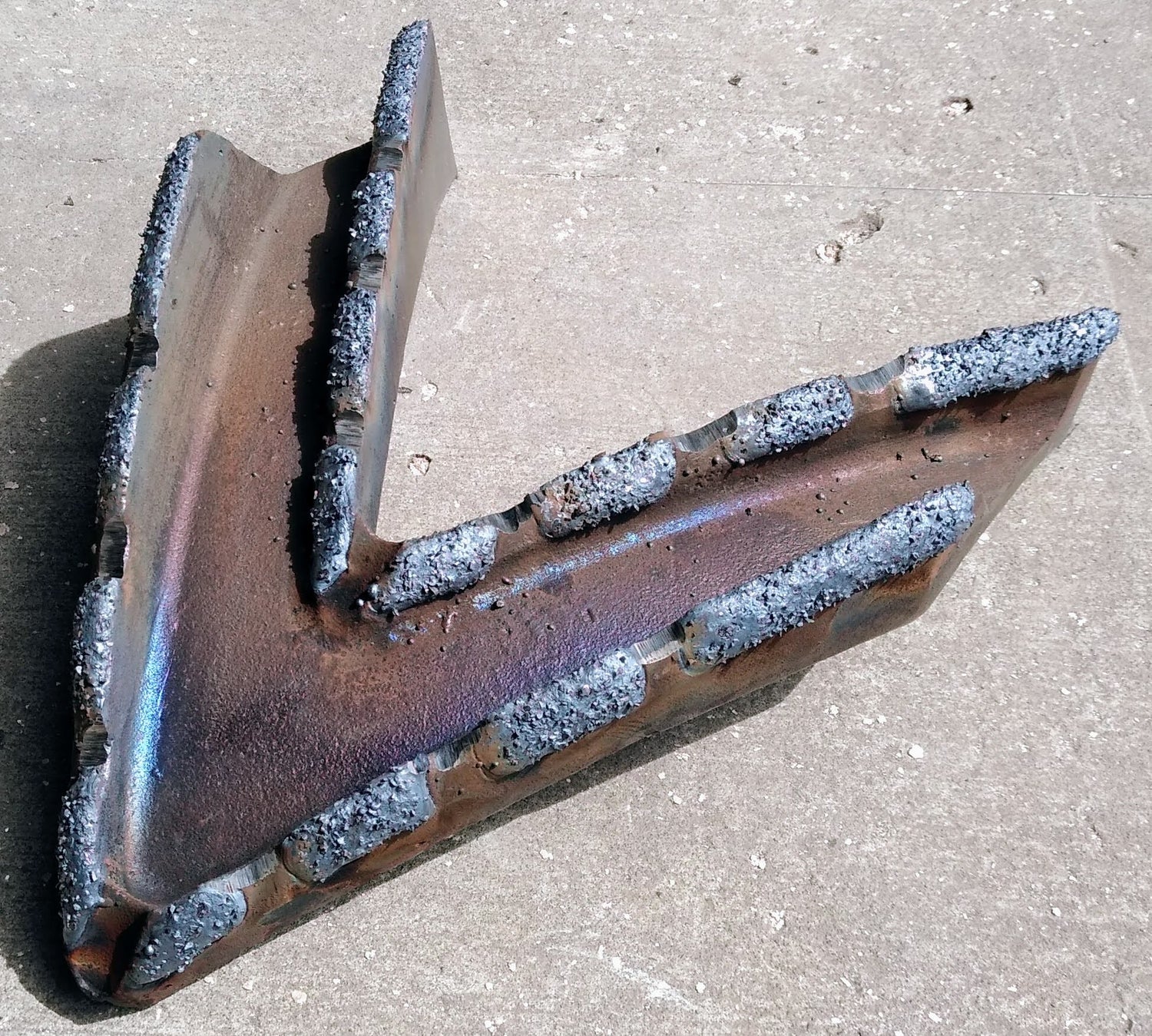
Debarker Flights
Handling logs is a tough business. We were able to offer our customer an embedded carbide (drop carbide) hardface that dramatically increased the wear life of their debarker flights.